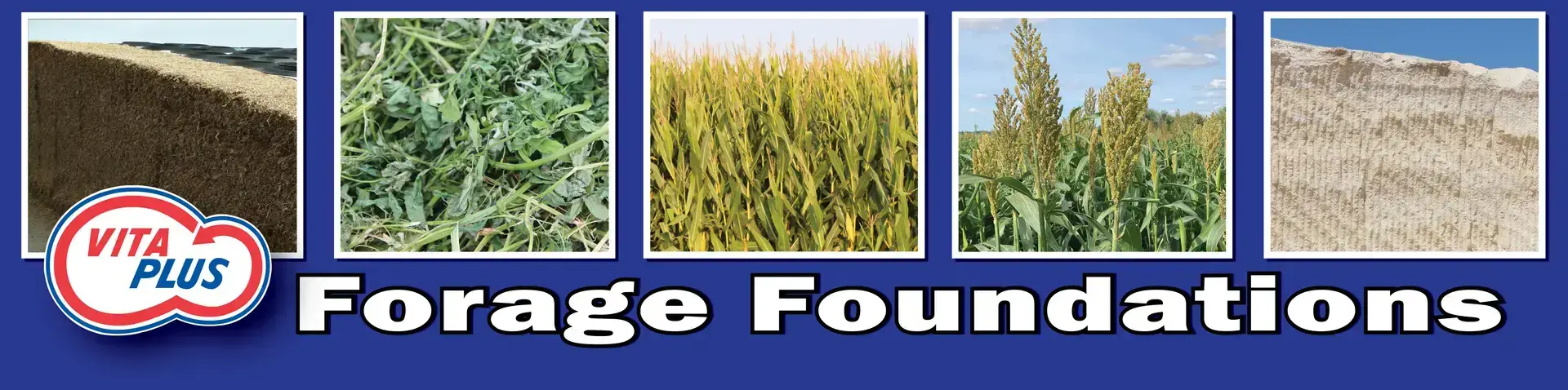
Wacek-Driver: From the Field to the Feedbunk: Are We Talking the Same Language?
Click to download presentation
It’s bound to happen…corn silage harvest is in full swing, harvesters are rolling, trucks are busy hauling and the pack tractors are moving back and forth when the nutritionist pulls in the driveway. They get out of the truck, walk up to the bunker, take a look at the freshly chopped forage and pronounce that the processor needs to be tightened and the cut lengthened.
“If that’s the time that we’re making those decisions we’re too late,” Chris Wacek-Driver told a room full of custom harvesters at the Vita Plus Custom Harvester Meeting.
According to Wacek-Driver, forage program manager for Vita Plus, those conversations need to be held now, long before harvest.
It helps to begin by looking at the entire system. “Why do we do what we do?” Wacek-Driver asked. “Is it about picking the right hybrid, chopping, processing, packing, storing and getting it fed right; or is it about the cow?”
“Sometimes we think about the end product incorrectly,” she continued. “Maybe it’s about milk, the consumer, or your family.”
To truly optimize the entire system, all those components need to come together.
Many times it feels more like a tug-of-war, she said. The demands can be long-cut or short-cut, adequate or optimal processing, cover more acres or slow down, less power or more power, fewer breakdowns or wear and tear.
“If you think corn silage is simple, you haven’t worked long enough in this field,” Wacek-Driver said.
Then she asked everyone to think of a customer of theirs, calculate how much tonnage they put up and put a $60 per ton value on it. Responses from the audience included $780,000, $1.4 million and $3.9 million.
“A lot of you probably knew what that value of forage is sitting out there,” she said. “What about your crew?”
Once the crew understands how valuable their job is, they will become more invested. “If you get your crew invested they will find you 5 percent more value,” she said.
Corn silage is unique in that it is a mix of grain and stover. Both parts are valuable and affect its nutritional value.
Because of its uniqueness and yield potential it has become a larger and larger portion of dairy cow diets.
The particle size affects both components of corn silage – the digestion of starch and physical effectiveness of fiber. It also affects packing density, fermentation, power and fuel consumption, and harvest time.
To harvest the best corn silage for each farm, the custom harvester, nutritionist, herd manager and agronomist need to work together and share their knowledge with one another.
“Everyone also needs to speak the same language,” Wacek-Driver said.
Length of cut can be measured in a number of ways. Harvesters set the cut through the feed rolls. Nutritionists measure it with a shaker box or a tape measure.
Everyone on the team needs to define length of cut and determine how it will be achieved. That should be done in the winter and spring, long before harvest. There should also be a Plan B in the event harvest is delayed by rain or the corn starts drying too fast in the field.
What the chopper is set at as length of cut does not always equate to final particle length. In one study, 55 samples with varying lengths of cut were measured to find the mean particle length. It was found that mean particle length only met what the chopper was set at 20 percent of the time.
In a study by Wacek-Driver, just over 20 percent met the set length of cut.
When comparing length of cut to the percentage of forage on the top screen of a shaker box, the relationship was stronger. More than 50 percent of the longer cuts had 15 percent on top screen.
To maximize starch digestion kernels should be processed. “It costs money not to have it processed,” she said.
For example, assume a high corn silage ration at $7 corn. If the processing score increases from 60 to 75, you could assume an extra $2 per ton of 35-percent dry matter corn silage. That doesn’t include extra milk production potential.
There are a number of factors that affect the processing score, including length of cut, processor design and wear, roll gap, aggressiveness, differential, capacity, hybrid, moisture and time.
When it comes to measuring processing, “we’re not as good as we think we are,” Wacek-Driver said. There needs to be a better way to measure it in the field.
Data from Dairyland Laboratories, Inc. indicates that processing has improved. In 2009, 33.6 percent of samples tested were poorly processed, 59.6 percent adequate and 6.8 optimum. In 2011, 22.7 percent of samples were poor, 59.9 percent adequate and 17.3 percent optimum.
To accomplish optimally processed corn silage can cost more in horsepower/fuel usage, wear and tear, and time.
If a harvester can’t tell the producer how much more it will cost, the producer will squeeze that margin. However, she said, if the harvester says it will cost 50 cents more to get a 70 percent processing score, up from 60, the producer will be more willing to pay it.
At one farm she works with, Wacek-Driver said the farmer estimates 50 cents more of wear and tear to get a longer length. The farmer pulls out the processor every day during harvest and uses feeler gauges to check roll gap. She said he feels that step makes him $250,000 more per year.
Just because a chopper is equipped with a processor doesn’t mean it will yield great silage. “You can have all the technology and design, but it’s going to be knowledge that moves us forward,” she said.
Efficiencies will continue to drive decisions. Harvesters need to have their costs in line in order to get paid for what they’re doing.
“Ultimately, for a system to work optimally, knowledge needs to flow between components of the entire system,” Wacek-Driver said. “Everyone needs to be on the team or the system won’t work optimally.”
Article written by Progressive Forage Grower Editor Karen Lee
Category: |
Forage Foundations |