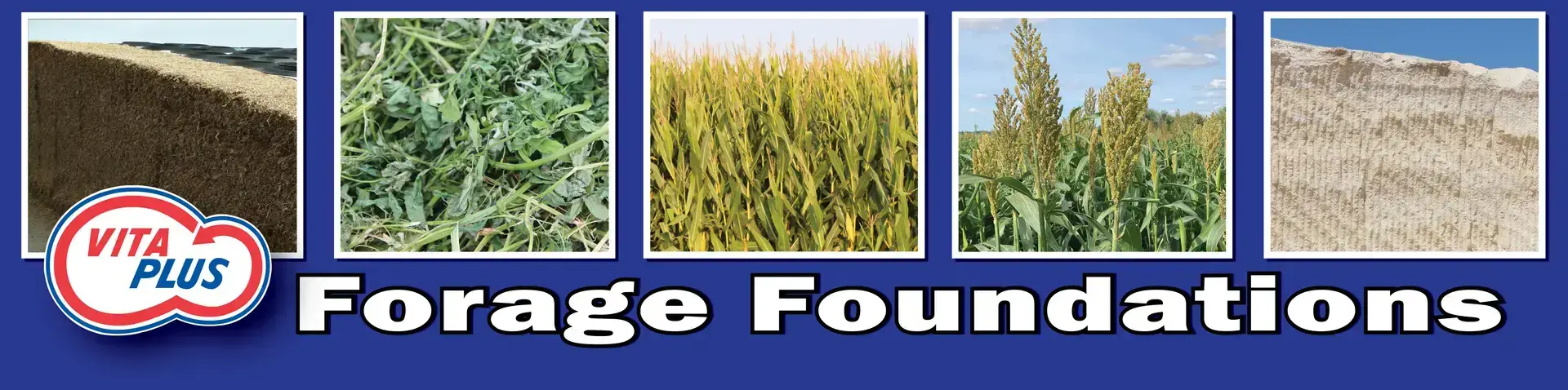
Advancements in silo plastic coverings

Quickly eliminating oxygen from silage and keeping it out during storage is integral to maintaining silage quality. During the upfront fermentation, rapid oxygen evacuation encourages a more efficient fermentation, which, in turn, minimizes fermentation losses. During storage, the more oxygen that seeps through the plastic, the more prone the silage is to spoilage.
To some degree, all plastics are permeable to oxygen. Using an oxygen barrier plastic will minimize oxygen seepage through plastics during storage. Initially, oxygen barrier plastics were made with a polyamide layer of plastic surrounded by polyethylene. However, these plastics were fragile and manufacturers moved towards producing oxygen barrier plastics with ethylene vinyl alcohol (EVOH).
Lower-quality oxygen barrier plastics made with polyamide are still widely available, and they are usually a lot less pliable and effective. Other products are also available that are clear but not oxygen barrier. Quality will vary greatly on these plastics.
Types of plastic systems
To help reduce spoilage, as well as the amount of labor needed, these plastic systems continue to be researched and upgraded.
Two-step system: Historically, oxygen barrier plastics have been part of a two-step system. The first layer applied is the clear oxygen barrier layer, which is susceptible to UV damage, followed by a second layer of traditional black-and-white plastic. The thinner, more pliable bottom layer can (and should) adhere to the contours of the silo surface. To encourage this, it is best to avoid tightly pulling the bottom oxygen barrier plastic when covering the silo and allow it to loosely fall and fill in the contours of the surface.
- Rolled-together plastic: One of the main drawbacks of the two-step system is the labor it requires. The recent advent of rolling together two layers of plastic on one roll (the clear plastic and the black-and-white plastic) allows for only “one” roll of plastic to be unrolled. While this appeals to many producers because of the time it saves to cover the silo, the biggest disadvantage of having the two plastic layers rolled together is the bottom layer is then pulled taut over the silage surface, which means it cannot properly or effectively adhere to the contours of the silage face.
- Stuck-together plastic: Another product that has hit the market is a silo plastic where both layers of plastic are rolled together and the bottom clear layer is temporarily adhered to the black and white plastic. In theory, when the plastic is unrolled and the silo is covered, the humidity from the silage mass would cause the plastics to separate, allowing the bottom layer to fall into the grooves of the silo surface. The issue here is two-fold. First, like the rolled-together plastic, the bottom layer cannot adhere to the contours of the silo surface, and second, the plastics often stay stuck together. Both issues result in channels being formed for oxygen to travel through.
- One-step system: Recently, a one-step system was developed where the oxygen barrier layer was melted into the black-and-white plastic, resulting in a thicker plastic. Within the last year, Silostop® has developed a one-step oxygen barrier plastic that is still quite thick (5mm thickness) but is also very pliable, and many producers are reporting quite a bit of success with preventing spoilage and saving labor by using this new one-step product.
In agriculture, we don’t have many areas where we can cut corners. However, the advent of new technologies offer a competitive advantage to those who choose to adopt them, which can save time, labor and dry matter losses.
Category: |
Forage Foundations Forage storage and management |