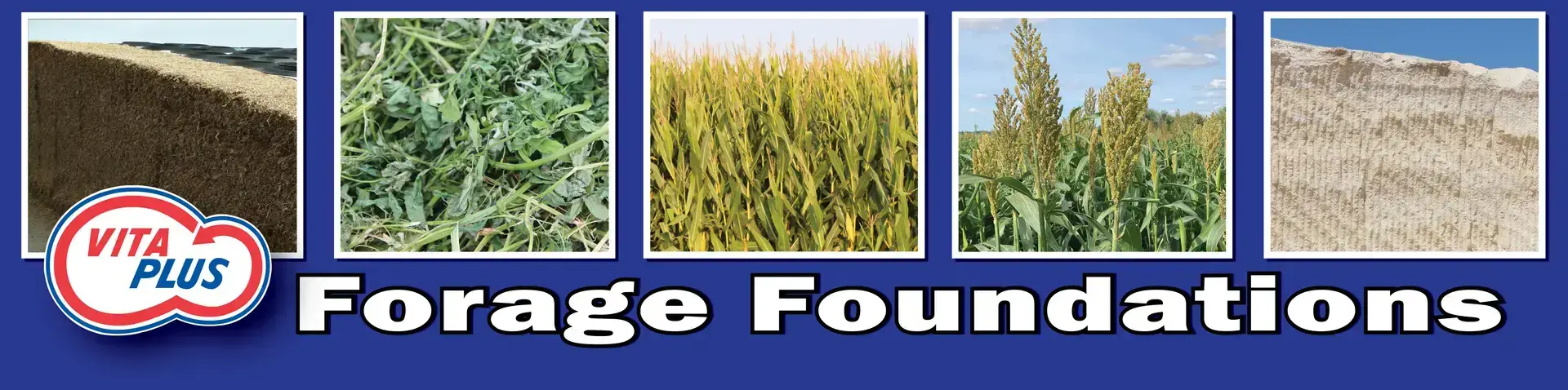
Tools to Expand Your Forage Team – John Brantsen, Vita Plus
Click here to download Brantsen’s PowerPoint Presentation.
When you’re facing tight harvest windows and a lot of fields to chop, putting up the highest quality forages is no small task. As John Brantsen, Vita Plus dairy specialist, discussed during his session at the Vita Plus Custom Harvester Meeting, improving forage quality can significantly impact profitability.
For large bunkers and piles, Brantsen said 15-percent shrink is “just a little better than average,” and he demonstrated what that means in terms of forage cost. If a farm harvests 1,000 tons of corn silage at a cost of $35 per ton, the total cost is $35,000. Fifteen-percent shrink means 850 tons are recovered. Dividing the total cost over 850 tons just increased the per-ton cost by $6 to $41 per ton. Thus, any step to reduce that shrink can have big payoffs.
According to Brantsen, “moisture trumps everything.” High dry matter (DM) leads to reduced packing density, a prolonged aerobic phase, less aggressive fermentation, greater infiltration of oxygen at feedout and increased DM loss. But low DM (high moisture) can lead to big challenges as well, including under-maximized yields and undesirable fermentation, especially in haylage, as well as wasted nutrients in effluent loss. He said he would not want to drop below 60 percent DM.
Brantsen recommended farmers and harvesters get together prior to harvest to set a “game plan.” Consider the field-to-farm traffic routes. Are roads wide enough for two-way traffic? Will you have to cross bridges, multiple field drives, tile intakes or wet areas? Answering these questions prior to harvest can keep crews moving safely until the job is done. He said crews can use aerial views, like those in Google Maps, to get a birds-eye view of the land and plan routes.
“That’s a valuable tool that probably isn’t used enough,” he said.
Brantsen emphasized the importance of kernel processing. Corn kernels can provide a significant energy contribution, but rumen microbes need a surface area to attach and utilize the starch. The better the processing, the higher the surface area. He said crews can evaluate kernel processing on the go. Fill a 32-ounce cup with fresh chop, pour out the sample on a truck bed, and count the number of whole kernels you find:
- 0 to 2 kernels: likely well processed
- 3 to 6 kernels: may be adequately processed
- Greater than 6 kernels: likely not adequately processed
Brantsen said he would wait to do this test until a field is opened. The chopper makes a lot of stops in the first few rows and the crop is pulled through the machine inconsistently. He said it’s better to wait and use the more consistent samples.
Farmers and crews should also discuss the desired particle size, which is different on every farm based on other forages available and production goals.
Brantsen also pointed to the importance of packing density. Unfortunately, density can’t be measured on the go, but you can have a good plan in place to help you achieve optimal density. He said, if you buy new equipment, think about how that will change the rate of harvest and how quickly forage gets put in the silo. The packing tractors need to match that pace.
Brantsen said the goal of a forage program is to “harvest high quality forage and maintain that quality from the field to the feedbunk.” A good plan, effective communication, and simple tools can help harvesting crews and farms achieve that goal.
Category: |
Equipment Forage Foundations Forage harvesting Technology and data management |