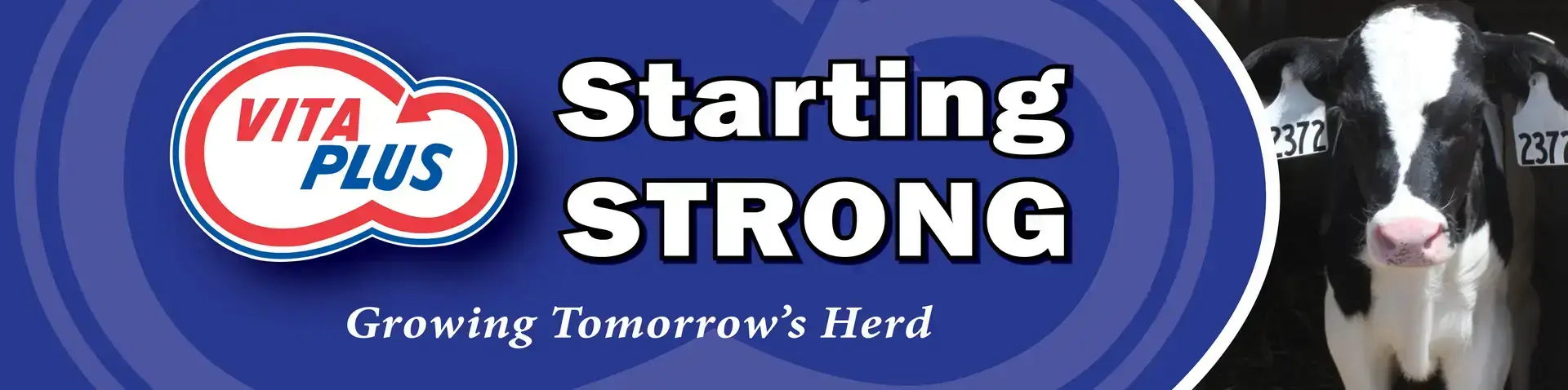
Safety is a Part of Your Business Too – Scott Hall
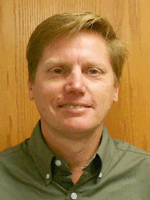
Farm safety has always been a concern to protect workers and family members. In the past, the Occupational Safety and Health Administration (OSHA) has placed most of its energy on construction and general industry. This approach recently changed to place more focus on the smaller employers that may or may not have the resources or personnel needed to develop comprehensive safety programs, train their employees and follow up with compliance/enforcement of these rules and regulations.
The OSHA Area Offices in Wisconsin also have developed a Local Emphasis Program (LEP) that targets dairy farms. They have been performing inspections on farms with more than 10 non-family employees. This does not mean that OSHA does not have jurisdiction over smaller farms; LEP is just targeting those with more than 10 employees.
Through LEP, OSHA is focusing on these 12 specific inspection items:
- Manure storage facilities and collection structures: Drowning hazards, operating equipment around waste storage, warning signs and equipment, hazardous gases
- Dairy bull and cow behavior/worker positioning: Hazards of working with/around dairy bulls or cows
- Electrical systems: Proper installation and maintenance of electrical equipment and buried or overhead power lines
- Skid-steer loader operation: Safe operation and maintenance of farm equipment and machinery
- Tractor operation: Safe operation and maintenance of farm tractors
- Guarding of power take-offs (PTOs): Working with or around power take-offs
- Guarding of other power transmission and functional components: Working with or around other unguarded equipment
- Hazardous energy control while performing servicing and maintenance on equipment: Preventing injuries from working on equipment or machinery such as maintenance, servicing, lockout-tagout (LOTO) program
- Hazard communication: Safety precautions for working with hazardous chemicals; training for all employees, requirements for material safety data sheets (MSDS), etc.
- Confined spaces: Safety precautions for working in spaces that have potential hazards from the configuration or simply entering the space (atmospheric, mechanical, electrical, entrapment, engulfment hazards)
- Horizontal bunker silos: Engulfment or struck-by hazards where employees perform ‘facing’ activities when removing silage from ground level or where employees climb on top of the silage to place or remove protective plastic covering and anchoring systems
- Noise: Hearing loss hazards when working with or around running agricultural equipment
With the busyness of spring just around the corner, now is a great time to take a comprehensive look at your farm and evaluate whether any of the above hazards exist on your farm. If they do, think about what training or safety measures you need to take to provide a safe working environment for your family and employees. Other areas to consider when developing or improving on-farm safety may include:
- Emergency action plan: What is the plan for an emergency (fire, severe weather, medical emergency, first aid, etc.) at your facility? Practice this with your employees. Do they all understand it, know what their responsibilities are, and know where to go in an emergency? Do the procedures work as planned?
- Fire extinguishers: Have at least one appropriate fire extinguisher located in each building, in every piece of machinery (tractors, skid-steers, loaders, etc.), and in any other location where a quick response to a fire may be needed. Fire extinguishers must be readily available, inspected regularly and recharged as needed.
- Posted “No Smoking” areas: All buildings and storage areas should be labeled as “no smoking” areas.
- Training: Document all training, whether it’s done in-house, by an outside trainer, at seminars, etc.
- Use available resources: Several agencies (OSHA, University of Wisconsin-Extension, WABA, Farm Bureau, community colleges, etc.) offer training and seminars in-person and online throughout the year.
Developing and implementing these programs takes a great deal of time, but is worth the investment when it helps to keep your team safe. Continued reviews of existing programs, regulations, inspections/audits, and training are required. Here are a few tips to help you take on this large project:
- The most difficult part of becoming compliant with OSHA regulations is getting started. It is not a one-time project that you can complete and then walk away.
- Don’t try to do everything at once. Pick a few items that are important to you or the industry (OSHA LEP is a good start) and tackle them first. Then move onto the next project.
- OSHA’s web page, OSHA Small Business, has several tools that can help answer many questions.
- Finally, ask for help. Most individuals in the safety field are very willing to help with regulation interpretation, program design or, at a minimum, point you in the right direction.
Category: |
Employee management Safety Starting Strong - Calf Care |